Advanced Welding WPS: Customizing Specifications for Complex Tasks
Advanced Welding WPS: Customizing Specifications for Complex Tasks
Blog Article
Unlocking the Power of Welding WPS: Techniques for Effectiveness and Safety And Security in Construction
In the realm of manufacture, Welding Procedure Specs (WPS) stand as the backbone of welding operations, dictating the needed steps for achieving both effectiveness and safety and security in the manufacture procedure. Understanding the intricacies of WPS is critical to using its full possibility, yet lots of organizations struggle to unlock the true power that exists within these papers (welding WPS). By diving right into the methods that optimize welding WPS, a globe of boosted productivity and heightened safety waits for those ready to discover the nuances of this essential facet of manufacture

Importance of Welding WPS
The value of Welding Procedure Requirements (WPS) in the fabrication industry can not be overstated. WPS serve as an important roadmap that details the needed actions to ensure welds are executed continually and properly. By defining essential criteria such as welding processes, products, joint designs, preheat temperatures, interpass temperatures, filler metals, and post-weld warm therapy demands, WPS offer a standard approach to welding that improves performance, top quality, and safety in manufacture processes.
Adherence to WPS helps in achieving harmony in weld quality, reducing the likelihood of issues or structural failures. This standardization likewise facilitates conformity with industry policies and codes, guaranteeing that produced frameworks meet the called for safety and security standards. Moreover, WPS documentation makes it possible for welders to replicate successful welding procedures, resulting in consistent results across different jobs.
In essence, the careful advancement and stringent adherence to Welding Procedure Requirements are extremely important for maintaining the stability of welded frameworks, safeguarding against prospective hazards, and upholding the credibility of fabrication companies for supplying high-quality services and products.
Key Components of Welding WPS
:max_bytes(150000):strip_icc()/MIG20welding20arc20in20action-2000-e8844d72f5094d408b5ab6f1c9436a4f.jpg)
Enhancing Effectiveness With WPS
When optimizing welding operations, leveraging the essential elements detailed in Welding Treatment Specifications (WPS) comes to be essential for streamlining processes and making the most of productivity. One method to boost efficiency with WPS is by very carefully picking the suitable welding parameters. By adhering to the certain standards provided in the WPS, welders can ensure that the welding equipment is set up correctly, leading to constant and top notch welds. Furthermore, complying with the pre-approved welding sequences described in the WPS can dramatically reduce the time invested on each weld, eventually enhancing overall performance.
Additionally, proper training and certification of welders in understanding and applying WPS can further boost performance. Making certain that all staff member are well-versed in interpreting and executing the WPS precisely can minimize errors and revamp, conserving both time and resources. Routinely evaluating and upgrading the WPS to include any kind of lessons discovered or technical developments can additionally add to efficiency enhancements in welding operations. By welcoming the standards stated in the WPS and continually seeking methods to maximize procedures, makers can accomplish higher effectiveness levels and premium outcome.
Ensuring Security in Fabrication
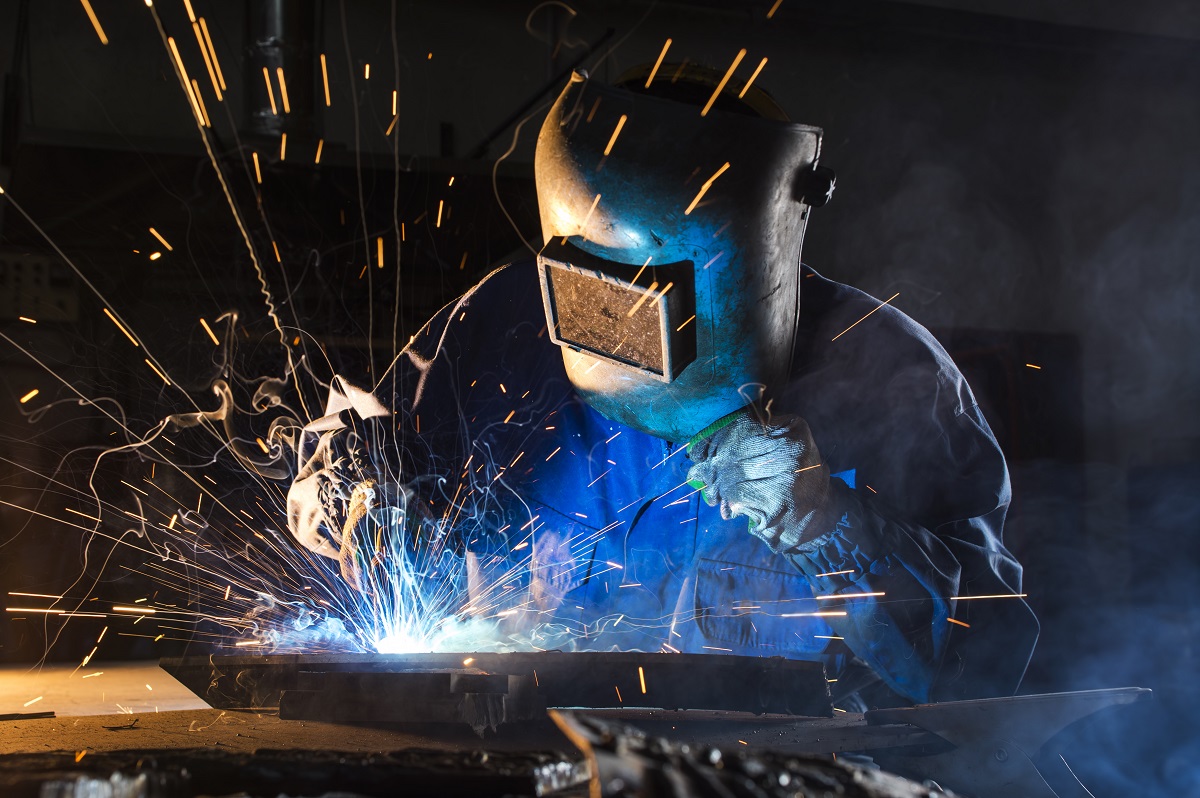
Safety methods in manufacture play an essential role in protecting employees and enhancing operational procedures. Making certain safety and security in construction entails a complex technique that includes different facets of the welding procedure. One fundamental element is the stipulation of personal Read Full Article protective devices (PPE) customized to the certain threats existing in the manufacture setting. Welders need to be geared up with ideal gear such as helmets, handwear covers, and safety garments to minimize dangers connected with welding activities.
Additionally, adherence to appropriate air flow and fume removal systems is vital in keeping a healthy and balanced work setting. Welding fumes have dangerous materials that, if breathed in, can posture severe health threats. Applying efficient air flow measures assists to reduce direct exposure to these unsafe fumes, advertising breathing wellness among employees.
Normal devices upkeep and evaluations are additionally important for making certain safety and security in fabrication. Defective equipment can lead to accidents and injuries, highlighting the importance of timely repair services and routine checks. By focusing on safety and security steps and cultivating a culture of recognition, fabrication centers can create a protected and productive workplace for their personnel.
Executing WPS Finest Practices
To boost operational efficiency and make sure high quality results in fabrication procedures, incorporating Welding Treatment Spec (WPS) finest techniques is extremely important - welding WPS. Implementing WPS finest methods includes thorough planning, adherence to sector criteria, and constant monitoring to guarantee optimum outcomes. Firstly, selecting the suitable welding procedure, filler material, and preheat temperature specified in the WPS is critical for attaining the desired weld high quality. Second of all, making certain that qualified welders with the necessary accreditations bring out the welding procedures according to the WPS guidelines is essential for uniformity and integrity. On a regular basis evaluating and upgrading WPS files to show any kind of process renovations or modifications in products is likewise an essential ideal method to maintain accuracy and significance. Additionally, giving thorough training to welding personnel on WPS requirements and ideal practices promotes a society of security and quality within the construction environment. By carefully carrying out WPS ideal techniques, fabricators can improve their procedures, decrease mistakes, and deliver exceptional products to meet client assumptions.
Final Thought
To conclude, welding WPS plays a critical function in guaranteeing efficiency and safety in manufacture procedures. By focusing on essential elements, boosting performance, and applying ideal practices, companies can enhance their welding procedures. It is necessary to prioritize safety and security measures to prevent crashes and guarantee a smooth manufacturing process. By complying with these techniques, services can unlock the complete capacity of welding WPS in their construction procedures. Read Full Article
In the realm of manufacture, Welding Procedure Specs (WPS) stand as the backbone of welding procedures, determining the needed steps for achieving both efficiency and safety in the manufacture process. By defining important specifications such as welding processes, materials, joint designs, preheat temperatures, interpass temperature levels, filler steels, and post-weld warm treatment requirements, WPS provide a standard strategy to welding that improves effectiveness, quality, and security in manufacture processes.
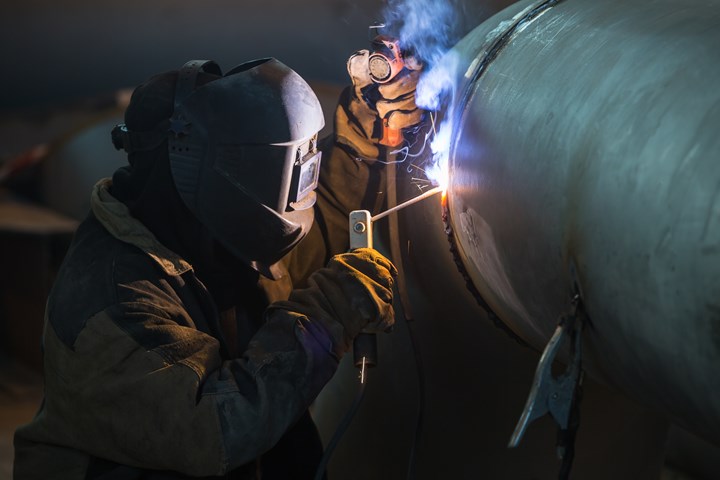
When enhancing welding operations, leveraging the crucial aspects described in Welding Treatment Specs (WPS) becomes vital for improving processes and making the most of performance. (welding WPS)
Report this page